|
Building Statistics
|
General Building Scope
Building Name: Largo Medical Office Building
Location: 14th Street S.W. Largo, Florida
Building’s Occupant Name: Diagnostic Clinic
Occupancy: Business Group B
Gross Square Footage: 154,240
Number of Stories: 6 stories above ground
Cost: $12.6 Million (not including equipment)
Construction Date: August 2008 - November 2009
Project Delivery Method: Design-Bid-Build
Owner and Developer: The Greenfield Group
Architect: Oliver, Glidden, Spina & Partners
Civil Consultant: N/A
Structural Consultant: McCarthy & Associates
Mechanical Consultant: Steve Feller, P.E. Inc.
Electrical Consultant: Steve Feller, P.E. Inc.
Plumbing Consultant: Steve Feller, P.E. Inc. |
|
Design Intent
Largo Medical Office Building is an expansion of the Largo Medical complex, designed to house an improved and centralized patient check-in area. At the same time the facility houses screening and diagnostic equipment, as well as office space for other future users.
Patient privacy is a major concern for facilities housing medical related activities. Oliver, Glidden, Spina & Partners answered this by clustering the screening and diagnostic spaces close to the dressing areas (Figure 1). The architect went a step further, to preserve privacy by compartmentalizing the building’s interior.
Oliver, Glidden, Spina & Partners designed the facility to be both financially and organizationally efficient. Offices and diagnostic spaces are grouped according to the field of treatment.
Though in the past internally efficient buildings didn’t incorporate a welcoming atmosphere, the Largo Medical Office Building is different. The facility attracts patients through the use of richly stained millwork, color selection, and traditional architectural elements. Expansive coffered ceilings (Figure 2) in the lobby and stone flooring allude to strength and customer trust, similar to banks during the early twentieth century.
|
|
 |
|
Figure 1, First Floor Diagnostic Space
Source: Oliver, Glidden, Spina & Partners |
|
|
|
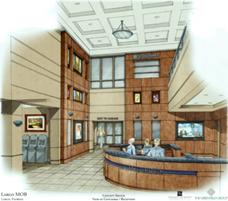 |
|
Figure 2, Lobby
Source: Oliver, Glidden, Spina & Partners |
Sustainability
During the design and construction of the facility, there was no consideration for sustainability.
Codes, Standards, and Zoning
National Codes:
Florida Building Code 2004 (Adaption of IBC 2003), AISC 13th Edition Steel Manual, ACI 318-05,
NFPA 70, NFPA 101, ANSI A17, National Electric Code 2005
Zoning and Local Codes:
City of Largo Zoning Designation: Community Redevelopment District-WBD
Largo Code of Ordinances
Historical Requirements
Does not apply
|
Building Envelope
Roofing System
LMOB has three roof levels: main roof, east emergency stairwell roof, and the overhang over the main entrance. There is only one roof type for all three roof levels, consisting of a 3-ply bituminous waterproofing applied over the insulated cast-in-place concrete (Figure 3). To ensure adequate rainwater drainage, the insulated cast-in-place concrete is sloped ¼” for every 12” horizontal.
The insulated cast-in-place concrete was used in-lieu of rigid insulation with stone ballast. One reason is that the facility is in a hurricane zone. What it means is, loose material can potentially become airborne projectiles and cause damage when there is a hurricane. The insulated concrete has sufficient mass to resist becoming airborne. In addition, the added mass counters the uplift wind force.
Façade
All façade components are designed to resist 130 mi/hr. winds, as required by the 2004 FBC. Reinforced CMU and impact resistant glazing are the primary components of the building façade. The façade is textured with stucco.
In order to secure the façade to the superstructure, angles and bolts were used. A notable characteristic of reinforced CMU is its high thermal mass.
To ensure impact resistance, uncoated laminated glass was used. The layers of the laminate include: (2) 1/4" thick heat strengthened glass sandwiching 0.3” of polyvinyl butyral (PVB). PVB serves to evenly distribute loads and prevent dangerous glass fragmententation.
|
|
|
|
Figure 3, Roof Detail
Source: Oliver, Glidden, Spina & Partners |
|
|
|
|
Figure 4, Wall Detail
Source: Oliver, Glidden, Spina & Partners |
|
Structure
McCarthy & Associates designed the Largo Medical Office Building’s (LMOB) superstructure. Supporting the superstructure are spread footings and strip footings. Spread footings are primarily utilized under steel columns, shear walls, and elevator shafts. On the other hand, strip footings are utilized to support the CMU building envelope.
Located in a hurricane zone, LMOB was designed to resist 130 mi/hr. winds. The main lateral system composes of 8” thick ordinary concrete shear walls. Extending to the roof level (86’ above ground level) shear walls are located at the emergency stairwells and elevator shafts. All (9) shear walls utilize two curtains of 60 ksi rebar and 3000 psi normal weight concrete. Each curtain utilizes #4 rebar to resist shear and #8 rebar for flexure.
LMOB’s composite slab and steel frame resist gravity loads. There are only slight variations to the bay sizes, but the most typical is 33’-0” x 33’-0”. The 5” composite floor slab is made up of 2” deep, 22 gauge composite metal decking and 3000 psi normal weight concrete. Shear studs (3/4”) were spot welded to the girder flanges to ensure partial composite action between the slab and girders. The typical girder size is W24x76. Girders primarily span in the East/West (longitudinal) direction. Only at the overhang above the lobby entrance and the loading dock area are the girders orientated differently.
|
Construction
LMOB is an expansion of the Largo Medical Center complex. Designed in 2007 and completed in 2009; the 155,000 ft2 facility is managed and constructed by The Greenfield Group. Overall the project cost $12.6 million, not including the equipment. All (6) floor levels are above grade, where the first floor houses diagnostic equipment for the hospital. The remainder of the facility is rented out as medical offices.
Limited number and size of access roads was a construction concern. Other medical facilities and the hospital at Largo Medical Complex require that the access roads remain uncongested and open, to ensure operational continuity. As a result the means to construct the building, as well as bringing materials and labor onto site require careful coordination between hospital personnel and the construction team.
|
MEP
HVAC
Direct Expansion (DX) with (2) cooling towers is the primary cooling system for LMOB. Cooling in each zone is controlled by a Variable Air Volume (VAV) box. This system doesn’t serve rooms with diagnostic equipment and the computer rooms. Instead the diagnostic equipment and computer rooms use refrigerant based DX system, utilizing variable frequency motors. The typical refrigerant based DX system used at LMOB, provides 5 tons of cooling per unit. In total, there are (6) units of the refrigerant based DX system. Heating LMOB is provided by resistant heating coils in each VAV box.
Conveying System
Vertical mechanical transportation at LMOB is provided by (4) elevators. One elevator is used for freight, this elevator has a 5000 lb. capacity and 350 ft/min. The other three are passenger elevators with a 3500 lb. capacity and 350 ft/min. All elevators are geared traction elevators manufactured by Otis. The elevators use 480/277V 3 phase power.
Electrical/Lighting
Power to LMOB is split into two systems 480/277V 3 phase and 208/120V 3 phase. The low voltage power, 208/120V 3 phase, is stepped down with the use of transformers. Diagnostic equipment, lighting loads, elevators, and the HVAC systems use 480/277V 3 phase power. Low voltage power is primarily utilized by the receptacles. To ensure electricity continuity to essential functions, a GTD20A emergency power relay system was installed.
All lighting systems use 277V 3 phase power. Most rooms except for the lobby, uses linear T8 fluorescent lighting. Two sizes of the recessed luminaire are 2x2 and 2x4. LED down lights and linear strips are used to highlight the lobby’s architecture.
Fire Protection
Fire protection systems at LMOB were designed according to the 2004 Edition of the Florida Building Code (FBC). LMOB used a wet standpipe system and is fully sprinkled. A 12” water main Feeding the active fire protection systems. To satisfy the 2-hour fire rating defined by the FBC, it is the floor assembly received sprayed cementitous fireproofing.
|
|